Hall
Magnetic measurement for dummies
The Hall effectA popular magnetometer technology, using a semiconductor plate. One injects current on one axis of the plate and measures a... More has been known since the late 19th century, and is the most common method for measuring medium to high fields, for a wide rangeThe range of a probe is defined by the minimum and maximum field strength it can measure. On an instrument,... More of applications. In fact, sensor applications – proximity sensors, rotation sensors, current sensors, etc. – are economically much more important than measurement applications, and have catapulted the Hall element into mass production.
How modern Hall probes work
11 minutes
Advantages
Nearly instantaneous
Readily integrated into electronic system
Constraints
PrecisionPrecision is how closely multiple measurements will be clustered. Also called reproducibility or repeatability. In everyday speech, often confused with... More less than NMRNuclear Magnetic Resonance. A resonance phenomenon seen when you irradiate a sample in a magnetic field with an RF field.... More or fluxmeterAn instrument that measures flux changes by integrating the voltage induced on a coil. More techniques
Careful calibrationDuring calibration, the instrument reading is compared to one or more references to verify its accuracy. The references themselves need... More required to compensate for voltage offset, temperature dependence and non-linearities
Angular dependence introduces hard-to-control measurement error
Magnetic measurement for dummies
A modern Hall element consists of a very thin slab of semiconducting material. If a current is injected parallel to the plate, a perpendicular magnetic field will drive the conductors to the left or right, thus causing a voltage differential between the left and right edges. This process is very nearly instantaneous; one can vary the sensitivity by varying the current; one can measure both positive and negative field components; and it is a simple affair to integrate such a sensor into a fully electronic measurement system.
The fine print: not suitable for dummies after all
This idyllic picture is disturbed by a number of annoying physical effects:
• A Hall element typically generates a voltage offset at zero field.
• The sensor response is only approximately linear.
• As the temperature increases, more conductors are available, and the device sensitivity changes.
• Hall plates also age, causing a long-term sensitivity driftThe gradual loss of an instrument's accuracy. NMR teslameters drift because their time base drifts; this can be easily checked and... More.
• The planar Hall effectA popular magnetometer technology, using a semiconductor plate. One injects current on one axis of the plate and measures a... More, whereby a field in the plane of the Hall plate creates a response, causes cross-talk between the vector components of the field.
• To the extent that the leads form current loops, moving a Hall probeThe actual sensor that is placed in the magnetic field. The NMR probe contains the NMR sample; the Hall probe... More in a strong field induces a voltage and biases the measurement.
• At cryogenic temperatures and with strong fields, the Hall conductivity becomes quantized.
Calibration …
To compensate for these physical effects, a Hall device needs to be carefully calibrated, and, to account for long-term driftThe gradual loss of an instrument's accuracy. NMR teslameters drift because their time base drifts; this can be easily checked and... More, it needs to be periodically recalibrated. Assuming the response is linear, the calibrationDuring calibration, the instrument reading is compared to one or more references to verify its accuracy. The references themselves need... More is generally performed at zero and the positive and negative limits of the measurement rangeThe range of a probe is defined by the minimum and maximum field strength it can measure. On an instrument,... More.
… calibration …
To calibrate at zero field, one can use a zero-Gauss chamber made out of extremely soft iron. For a more precise zero, a coil that exactly offsets the (local) earth’s magnetic field is required. To calibrate the high end of the rangeThe range of a probe is defined by the minimum and maximum field strength it can measure. On an instrument,... More, a high-field reference magnetA magnet used for calibrating a magnetometer. Reference magnets are often controlled or even regulated by an NMR teslameter. More is required. For the ultimate reference, the magnet is controlled or even regulated by NMRNuclear Magnetic Resonance. A resonance phenomenon seen when you irradiate a sample in a magnetic field with an RF field.... More.
… and more calibration
If the response is significantly non-linear, a calibrationDuring calibration, the instrument reading is compared to one or more references to verify its accuracy. The references themselves need... More at one or more intermediate field values is required. If the instrument has several sensitivity ranges, it should be calibrated at every rangeThe range of a probe is defined by the minimum and maximum field strength it can measure. On an instrument,... More. To compensate for temperature effects, the entire calibrationDuring calibration, the instrument reading is compared to one or more references to verify its accuracy. The references themselves need... More needs to be repeated at at least two temperatures. And if one wants to compensate for the planar Hall effectA popular magnetometer technology, using a semiconductor plate. One injects current on one axis of the plate and measures a... More or other sources of cross-talk, a very complicated 3D calibrationDuring calibration, the instrument reading is compared to one or more references to verify its accuracy. The references themselves need... More and de-convolution becomes necessary.
The uncontrolled error source
One source of error escapes the best sensor technology and calibrationDuring calibration, the instrument reading is compared to one or more references to verify its accuracy. The references themselves need... More procedure: angular positioning. Even the best measurement laboratories are obliged to send the Hall sensor on a harrowing journey from calibrationDuring calibration, the instrument reading is compared to one or more references to verify its accuracy. The references themselves need... More jigIn our context, refers to a mechanical structure that allows a probe to be placed in known locations in the... More to measurement jigIn our context, refers to a mechanical structure that allows a probe to be placed in known locations in the... More, with nasty gangs of rolls, pitches and twists just waiting to cumulate at every move. The situation is of course infinitely worse for a handheld device. It is for this reason that Metrolab advocates using three-axisThe magnetic field is a three-dimensional vector quantity. A single Hall element only measures one component. A three-axis Hall instrument has... More sensors that minimize the loss of information.
More technologies
Products
Related products
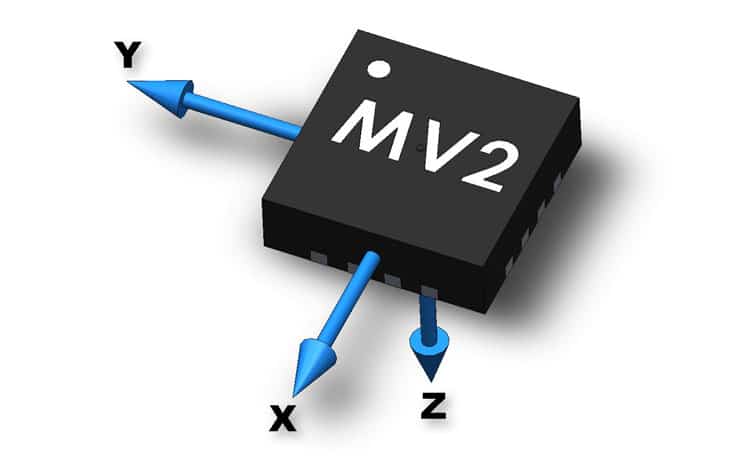
MagVector™ MV2 Magnetometer
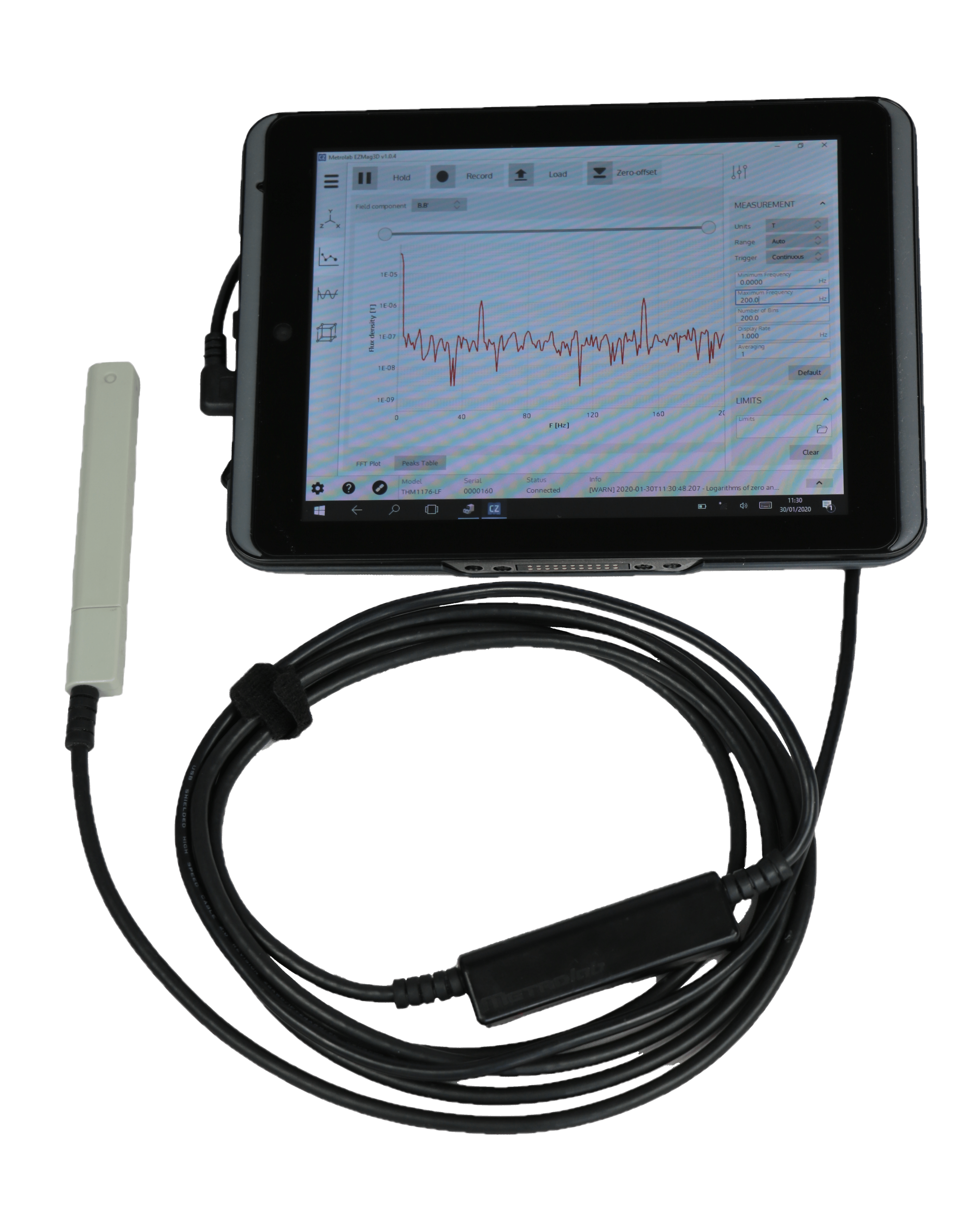
THM1176 Hall Magnetometer
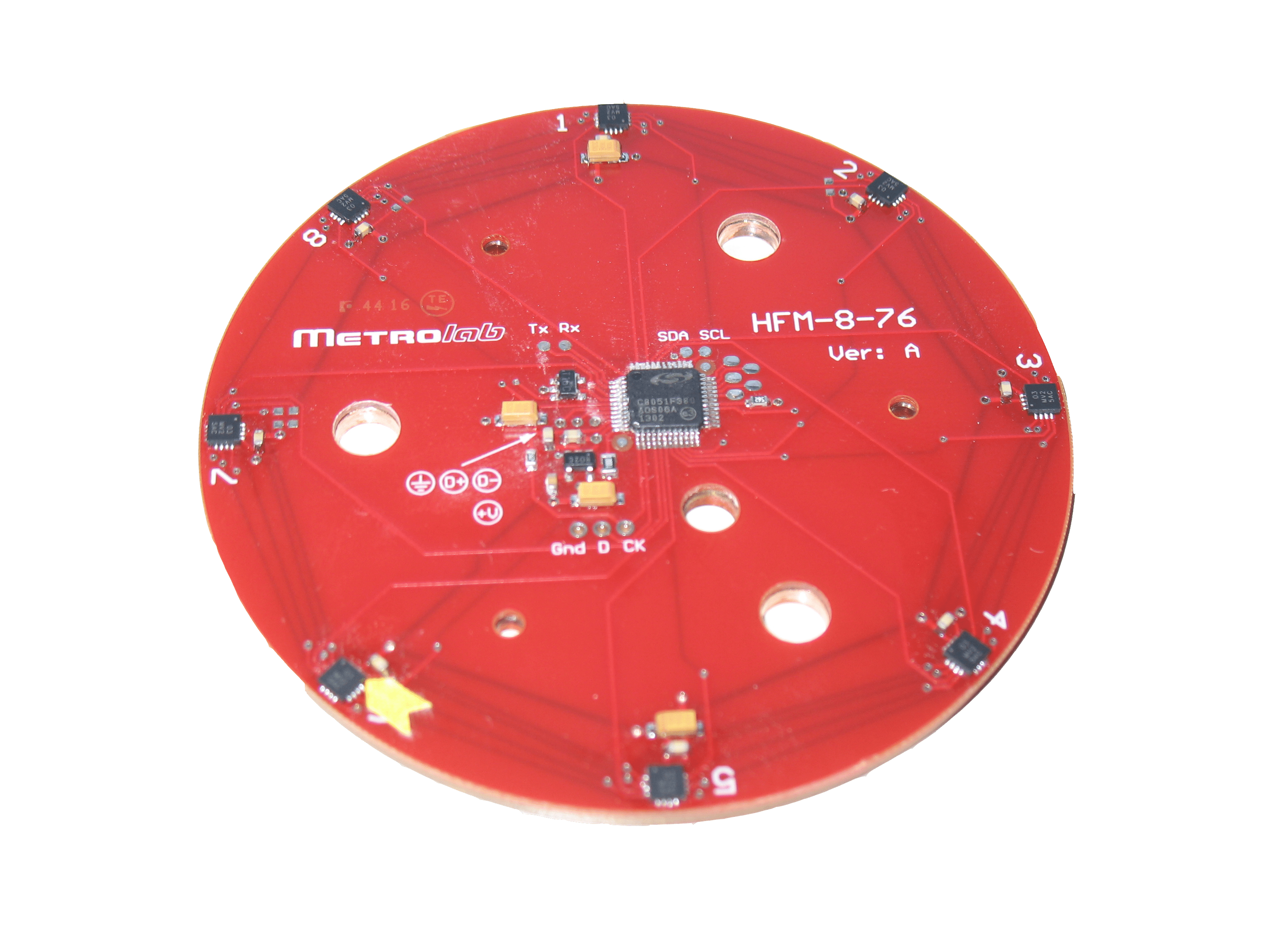
HMC9076 Hall Magnetic Camera
Applications
Related applications
Science
General science & engineering
MRI
Fringe fieldThe field around a magnet, not in the gap or bore. More measurement
OEM
Magnetic background monitoring
Want to know more ?
Contact us for more information !
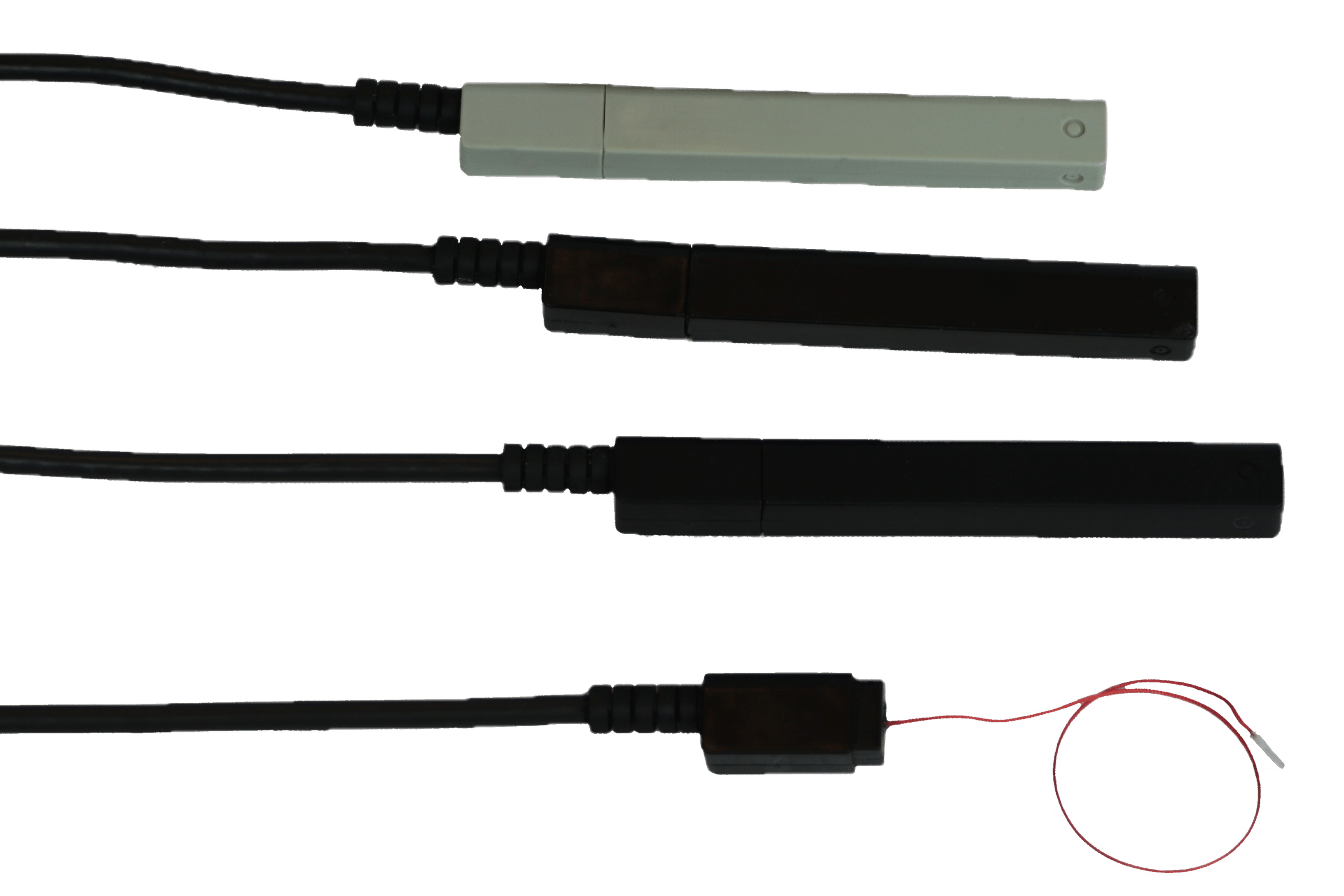